Activated carbon screening meets screening needs, only one stainless steel rotary vibrating screen is needed.
Post Date: 2025-02-04
Activated carbon is a crucial material used in a wide range of industries, from water and air purification to gold recovery and pharmaceutical applications. Its ability to adsorb impurities makes it a highly effective solution for various processes. However, ensuring the quality and consistency of activated carbon requires efficient screening to separate fine particles and impurities. For this purpose, the stainless steel rotary vibrating screen offers an ideal solution, meeting the demanding screening needs of activated carbon production and processing.
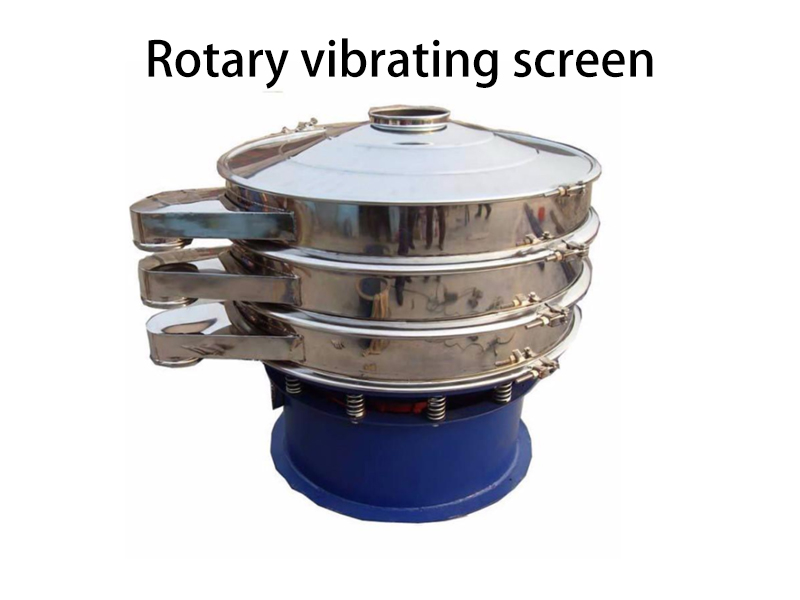
The Role of Activated Carbon in Various Industries
Activated carbon is produced by heating carbon-rich materials (such as coal, wood, or coconut shells) in the presence of a gas that creates a network of pores, increasing its surface area and adsorptive capacity. It’s used for:
- Water and Air Filtration: To remove pollutants, chemicals, and toxins.
- Gold Recovery: For extracting gold from ores during mining operations.
- Pharmaceuticals: In drug formulations and detoxification.
- Food and Beverage: For purifying liquids and removing impurities.
Given the diverse applications, it’s vital that activated carbon meets specific quality standards, particularly in terms of particle size, purity, and uniformity.
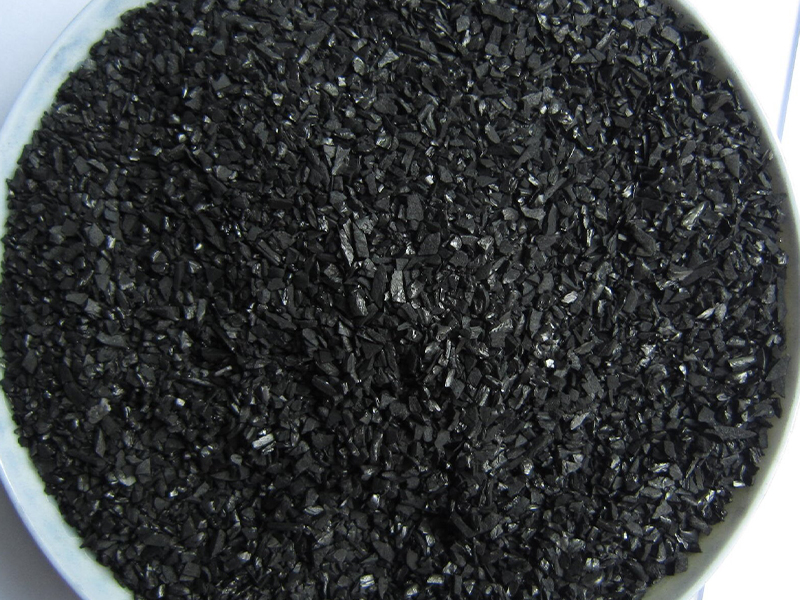
The Need for Efficient Screening of Activated Carbon
The production and handling of activated carbon often involves processing granular or powder forms. As activated carbon is prone to dust, clumps, and particle size variation, effective screening is necessary to achieve the desired consistency for each application. Without proper screening, activated carbon can have too many fine particles, which could reduce its effectiveness in adsorption processes or cause issues in downstream applications like filtration.
Screening activated carbon serves several purposes:
- Particle Size Classification: To separate fine particles and oversized materials, ensuring uniformity.
- Dust Removal: To eliminate excessive fines that may cause clogging or reduce the material’s adsorption capabilities.
- Purity Maintenance: To remove contaminants or impurities that may interfere with the activated carbon’s performance in critical applications.
Why Stainless Steel Rotary Vibrating Screens are the Perfect Choice
A stainless steel rotary vibrating screen is an ideal tool for screening activated carbon. Here’s why it meets the specific needs of this material:
1、Durable and Corrosion-Resistant Construction
Activated carbon screening requires robust equipment capable of handling high-volume materials over long periods of time. Stainless steel rotary vibrating screens are built to last and withstand the demanding nature of activated carbon processing. The corrosion-resistant properties of stainless steel ensure that the screen maintains its integrity even in harsh conditions, particularly in environments where moisture or chemicals may be present.
2、Efficient Screening Performance
Rotary vibrating screens use a three-dimensional vibration motion (horizontal, vertical, and inclined) that ensures efficient material flow and thorough separation. This motion is particularly effective for screening activated carbon, as it allows fine particles to pass through the mesh while oversized materials are kept separate. The circular motion of the screen promotes material agitation, which enhances the screening process and ensures a consistent output of screened carbon.
3、Customization for Particle Size and Throughput
One of the standout features of stainless steel rotary vibrating screens is their ability to be tailored to specific needs. The mesh size can be adjusted to suit the particle size of the activated carbon, and the vibration amplitude can be fine-tuned to optimize throughput. Whether processing fine powders or larger granules, rotary vibrating screens can handle various material sizes and throughput volumes efficiently, ensuring that the activated carbon meets its specifications.
4、Self-Cleaning Functionality
In industries where activated carbon is used in large quantities, the equipment used for screening needs to operate continuously without clogging or frequent maintenance. Many stainless steel rotary vibrating screens are equipped with self-cleaning mechanisms, preventing the mesh from getting clogged with fine carbon dust or other particles. This ensures that the screening process remains efficient and reduces the need for manual cleaning, keeping downtime to a minimum.
5、Minimal Maintenance
Stainless steel rotary vibrating screens are designed for minimal maintenance, which is particularly valuable in large-scale operations. Regular maintenance checks are simple and quick, typically involving visual inspections and mesh replacements if necessary. With a durable stainless steel frame and high-quality components, these screens can operate for extended periods with only minor interventions.
6、Hygienic and Safe Processing
In industries like pharmaceuticals and food, cleanliness is critical. Stainless steel is easy to clean and sterilize, ensuring that there is no contamination during the screening process. The smooth surface of the stainless steel frame and mesh helps prevent the accumulation of material residues, reducing the risk of cross-contamination and maintaining the purity of activated carbon.
The Benefits of Using a Stainless Steel Rotary Vibrating Screen for Activated Carbon Screening
1、Increased Productivity: With continuous operation and high throughput capabilities, stainless steel rotary vibrating screens can process large volumes of activated carbon with minimal downtime.
2、Cost-Effectiveness: While the initial investment may be higher compared to other screening equipment, the longevity, efficiency, and minimal maintenance requirements of stainless steel rotary vibrating screens make them a cost-effective solution in the long run.
2、Consistent Product Quality: By ensuring uniform particle size and removing impurities, these screens help maintain the high quality and effectiveness of activated carbon, which is essential for its use in critical applications like filtration and purification.
4、Improved Process Control: The ability to adjust screening parameters (such as mesh size, vibration intensity, and screen inclination) allows operators to fine-tune the process to achieve the desired results, improving overall process control and product consistency.