In the evolving landscape of industrial material processing, precision, flexibility, and adaptability are critical. Whether handling viscous slurries, ultra-fine powders, or granular materials, manufacturers require a screening solution that can meet diverse separation needs without compromising efficiency. The Rotary Vibrating Screen (also known as a rotary vibro sifter or vibro separator) is designed to fulfill exactly that role.
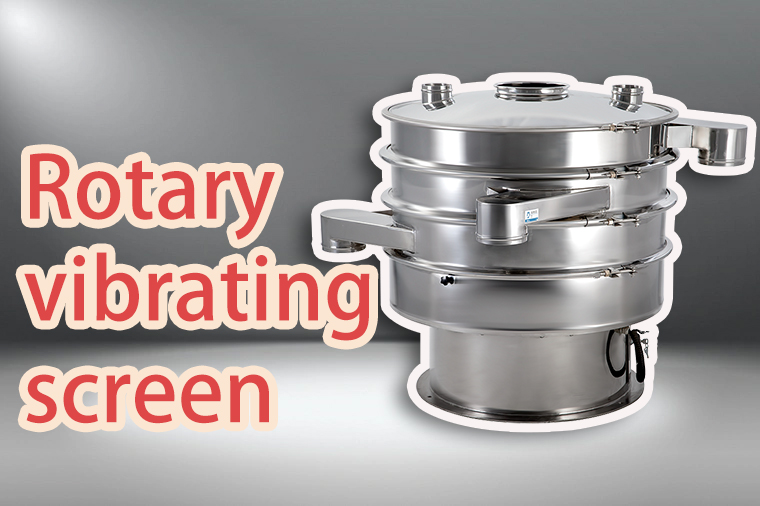
This high-precision screening equipment is widely used in industries such as food processing, chemicals, pharmaceuticals, ceramics, metallurgy, mining, and wastewater treatment, where accurate classification or filtration of materials is essential.
Multi-Layer Screening for Maximum Efficiency
A standout feature of the rotary vibrating screen is its multi-layer capability. The machine can be configured with one to five screen decks, allowing it to simultaneously classify materials into two to six different grades or sizes. This multi-tiered screening design enables users to complete complex sorting operations in a single pass—saving both time and energy.
Each screen layer can be fitted with mesh of different sizes depending on the desired output, allowing for precise separation of particles or filtering of liquids at multiple levels. Whether you’re separating coarse particles from fine powders, or filtering solid impurities from slurry, the rotary vibrating screen provides highly consistent results.
Ideal for Slurry, Powder, and Granule Screening
While many screens are optimized for either wet or dry materials, the rotary vibrating screen offers exceptional performance across both categories, including:
- Slurry Screening: For liquid-based materials such as ceramic slurry, paint, wastewater, pulp, or latex, the rotary screen ensures efficient filtration by removing oversized particles and impurities. The unit can handle both low- and high-viscosity fluids with equal ease.
- Powder Separation: Fine powders used in industries such as pharmaceuticals, chemicals, and food can be sorted into multiple grades with minimal dust generation and material loss.
- Granular Material Sorting: Granules of various sizes can be accurately separated, improving product uniformity and downstream processing efficiency.
This makes the rotary vibrating screen a multi-purpose tool across a wide range of industrial applications.
Key Advantages of the Rotary Vibrating Screen
1. Flexible Design
With options for 1–5 screen layers and 2–6 output grades, the machine can be adapted to suit virtually any screening requirement.
2. High Screening Precision
The screen operates with a three-dimensional vibration motion—combining vertical, horizontal, and inclined movements—to ensure thorough material stratification and highly efficient separation.
3. Fast and Easy Mesh Replacement
Modular screen frames make it simple to change mesh sizes or clean the equipment. This is especially important in applications where frequent product changes occur.
4. Compact and Low-Noise Operation
Despite its powerful screening ability, the rotary vibrating screen maintains a small footprint and quiet operation, making it suitable for installation in noise-sensitive or space-constrained environments.
5. Sanitary and Safe Construction
In sectors like food and pharmaceuticals, hygiene is critical. Rotary vibrating screens are typically made of stainless steel, with options for polished, easy-to-clean surfaces, sealed covers, and dust-free operation, ensuring compliance with sanitary standards.
6. Energy-Efficient Performance
The machine consumes relatively low power while delivering high output, which is especially beneficial in continuous production lines.
Widely Used Across Industries
Due to its versatility, rotary vibrating screens are found in diverse sectors, including:
- Food & Beverage: For sieving flour, sugar, starch, spices, juice pulp, etc.
- Chemical & Petrochemical: For powder separation, resin filtration, pigment classification.
- Pharmaceutical: For grading active ingredients, excipients, and coating materials.
- Ceramics & Glass: For filtering ceramic slurries or glass powder.
- Environmental: For solid-liquid separation in wastewater treatment.