In the coal mining and preparation industry, coal gangue—a byproduct formed during the extraction and processing of coal—poses both a challenge and an opportunity. It must be efficiently crushed to be reused as raw material in construction, power generation, or cement production. However, due to its hard, brittle, and layered structure, coal gangue is not easily processed by traditional crushing equipment.
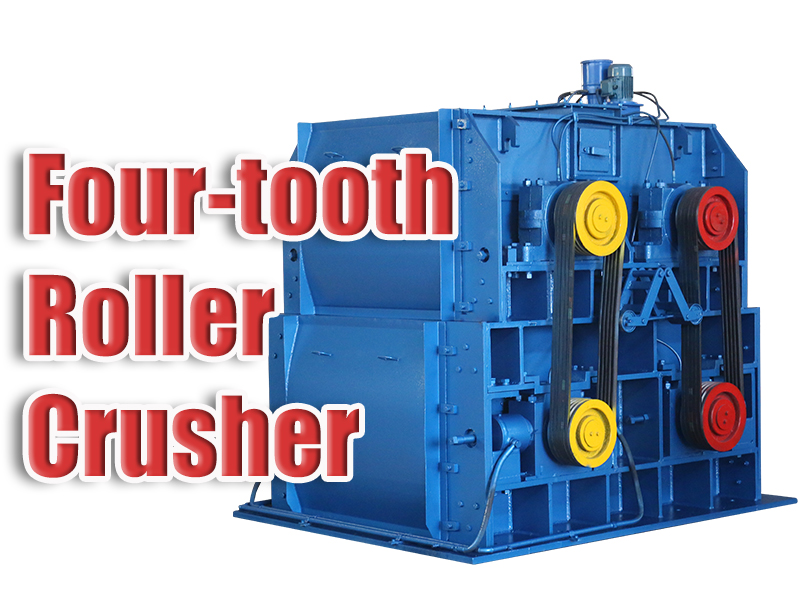
The four-tooth roll crusher offers a high-efficiency, intelligent alternative that excels in crushing coal gangue with minimal over-crushing, reduced wear, and superior particle control. It is an ideal solution for enterprises seeking stable, energy-efficient, and environmentally conscious material processing systems.
Purpose-Built for Coal Gangue: Composite Crushing, Not Impact
Unlike conventional crushers that rely heavily on impact or high-speed hammering, the four-tooth roll crusher uses a composite crushing method. This approach involves the use of shear, compression, and inter-particle friction, rather than violent impact forces. This has two immediate benefits:
- No secondary fragmentation: The coal gangue is broken cleanly in a single step without generating excess fines or powder, preserving material integrity.
- Low over-crushing rate: Unlike impact crushers that tend to pulverize material, this crusher delivers uniform particle size and avoids unnecessary reduction.
This method is especially effective with coal gangue’s layered and brittle characteristics, providing a clean fracture without the drawbacks of repeated crushing.
Stable, Intelligent, and Reliable Performance
The four-tooth roll crusher is engineered with a focus on process stability and intelligent control. Its robust mechanical structure and automated systems allow it to operate continuously under varying loads without interruptions. This is particularly important in gangue crushing, where inconsistent feed quality can lead to equipment clogging or wear in less capable machines.
Through intelligent load monitoring and hydraulic adjustment, the crusher maintains optimal roller spacing and feed rate, even as material conditions fluctuate. This leads to smoother operation, reduced energy consumption, and longer equipment life.
Even Feeding, Extended Lifespan
One of the most overlooked but vital aspects of effective crushing is uniform feeding. The four-tooth roll crusher incorporates a feeding system that ensures even distribution of material across the roller surface. This eliminates localized pressure buildup, which is a common cause of premature wear in conventional crushers.
As a result, abrasion is minimized and the life span of core components such as teeth, rollers, and liners is significantly extended. For operators, this means fewer shutdowns, reduced maintenance costs, and improved overall productivity.
Superior Output Control: Consistent, Adjustable Particle Size
The crusher’s advanced design ensures excellent particle size control, allowing discharge size to be customized according to downstream requirements. Whether the end use is in road base, cement kilns, or bricks, the equipment delivers a stable and uniform output without the dust and fines associated with impact crushers.
This controlled crushing ability not only improves the quality of the final product but also enhances environmental performance by reducing dust generation at the source.
Key Advantages at a Glance
- No Secondary Crushing: Composite fracture ensures clean, single-pass crushing.
- Low Over-Crushing Rate: Delivers consistent particle size, minimal fines.
- Intelligent and Reliable Operation: Adapts to load changes and varying material characteristics.
- Even Material Distribution: Prolongs roller and component life.
- Environmentally Friendly: Reduced dust generation and lower energy consumption.
- Optimized for Coal Gangue: Specifically designed to handle brittle, layered materials effectively.