Gaofu ultrasonic vibrating screen is used for calcium oxide screening, increasing the output by 2~5 times.
Post Date: 2025-02-04
In industries that process fine powders, such as chemical manufacturing, materials like calcium oxide (CaO), commonly known as quicklime, can pose significant challenges during screening. Calcium oxide is highly reactive, especially when in fine powder form, and its tendency to clump or adhere to screens can result in clogged meshes and inefficient screening. This leads to reduced throughput, increased downtime, and lower overall productivity.
Fortunately, the Gaofu Ultrasonic Vibrating Screen offers a powerful solution to these challenges. By integrating ultrasonic vibration technology into traditional vibrating screens, the Gaofu ultrasonic vibrating screen can increase calcium oxide screening output by as much as 2 to 5 times. Here’s a breakdown of how this technology works and why it can dramatically improve screening efficiency and capacity.
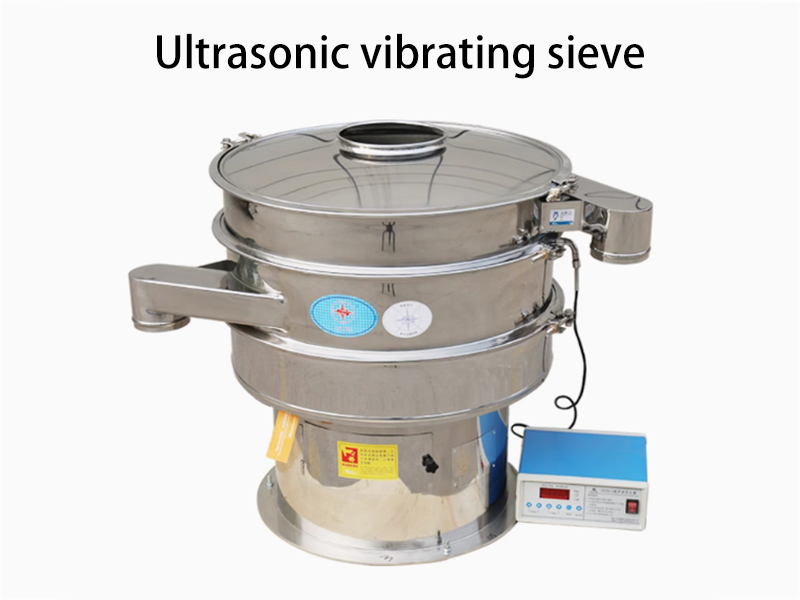
Challenges in Calcium Oxide Screening
Calcium oxide has a high tendency to agglomerate or form lumps, especially when exposed to moisture in the air. These clumps can quickly clog conventional vibrating screens, resulting in a blockage that limits material flow, reduces separation efficiency, and often leads to downtime as operators clean the screen.
Additionally, calcium oxide is an abrasive material, and prolonged exposure to traditional screens can cause wear and tear, affecting screen life and the overall cost of maintenance. Fine particles in calcium oxide may also be prone to sticking to the screen mesh, which further impedes material flow and reduces the overall throughput.
To overcome these challenges, more advanced technologies such as ultrasonic vibration are being increasingly applied in material screening processes.
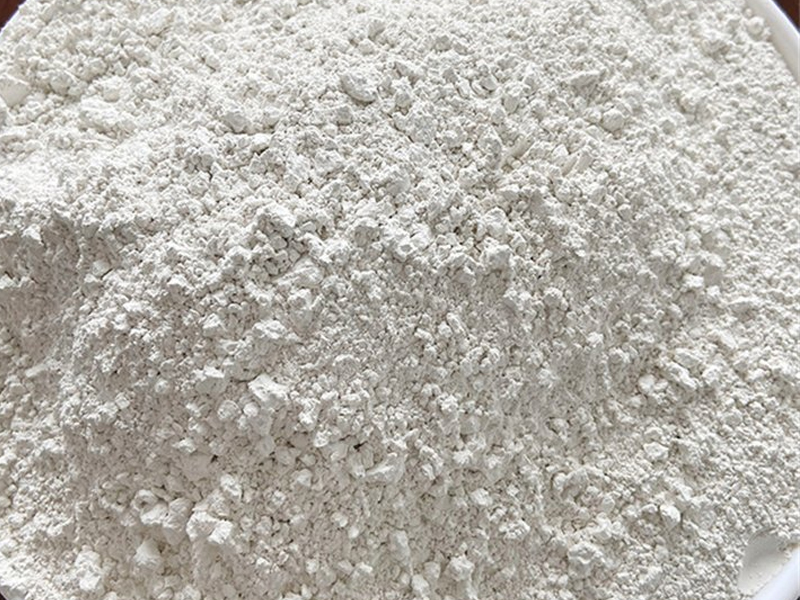
How Gaofu Ultrasonic Vibrating Screen Works
The Gaofu Ultrasonic Vibrating Screen operates by adding an ultrasonic transducer to a standard vibrating screen. This transducer generates high-frequency sound waves (typically between 20-40 kHz), which are then applied to the screen mesh. The ultrasonic vibrations create a fine, high-frequency oscillation on the surface of the screen, helping to break up agglomerated or sticky particles and reduce friction between the material and the mesh.
This technology can provide several benefits when screening materials like calcium oxide:
- Prevents Clogging: The ultrasonic vibrations prevent calcium oxide particles from sticking together and adhering to the mesh, keeping the screen surface clear and ensuring uninterrupted material flow.
- Enhances Material Flow: The vibrations created by the ultrasonic waves break up material clumps, allowing even fine or sticky particles to pass through the mesh more easily, which increases screening efficiency.
- Reduces Mesh Blockage: Fine calcium oxide particles that might normally stick to the mesh are prevented from doing so by the ultrasonic energy, leading to faster and more efficient separation.
- Improves Screening Precision: Ultrasonic vibrations ensure that even fine particles, which may otherwise be difficult to separate, are effectively sorted and classified. This leads to a higher-quality output and more precise screening.
Impact on Calcium Oxide Screening Output
The Gaofu Ultrasonic Vibrating Screen can significantly increase the output of calcium oxide screening by 2 to 5 times compared to traditional screening methods. Here’s how:
- Faster Screening: The ultrasonic vibrations help keep the calcium oxide material moving smoothly through the screen, reducing blockages and preventing material from backing up. This results in faster processing times and higher throughput.
- Higher Separation Efficiency: Ultrasonic vibrations reduce the tendency for calcium oxide particles to agglomerate, allowing for better separation of fine particles from coarser ones. This ensures that the final product is of a higher quality and purity.
- Reduced Downtime: With fewer blockages and material build-up on the mesh, the need for frequent screen cleaning and maintenance is greatly reduced. This results in less downtime and more continuous production, boosting overall productivity.
- Extended Screen Life: Since the ultrasonic vibrations reduce friction and wear on the mesh, the lifespan of the screen is extended, reducing maintenance costs and ensuring a longer-lasting system.
Additional Benefits of Gaofu Ultrasonic Vibrating Screen
Apart from increasing screening output, the Gaofu Ultrasonic Vibrating Screen offers several other advantages for processing calcium oxide:
- Versatility: The ultrasonic vibrating screen is highly adaptable and can be used for screening a wide range of materials, not just calcium oxide. Its ability to handle fine powders, sticky materials, and even fragile substances makes it a versatile solution for various industries.
- Cost Efficiency: While the initial investment may be higher than traditional vibrating screens, the reduction in downtime, maintenance costs, and increased production capacity quickly pays for the system in the long run.
- Improved Product Quality: The enhanced separation and classification of materials ensure that the final output is of a higher standard. In applications where the purity of the material is crucial, such as in the chemical industry, this quality boost is invaluable.
Application of Gaofu Ultrasonic Vibrating Screen in Calcium Oxide Processing
In the production of calcium oxide, the material is typically processed in large volumes, and high screening efficiency is crucial for maintaining consistent quality and throughput. Here are a few common applications where the Gaofu Ultrasonic Vibrating Screen can play a crucial role:
- Fine Screening of Calcium Oxide Powder: For applications requiring the separation of fine calcium oxide particles, the ultrasonic vibrating screen can ensure that even the finest particles pass through without clogging, enabling more precise separation.
- Removal of Impurities: Ultrasonic vibration technology can help in removing any unwanted impurities from the calcium oxide material by ensuring that only the desired particle size passes through the mesh.
- Handling Moist or Sticky Calcium Oxide: Calcium oxide, when exposed to moisture or humidity, can become sticky or clump together. The ultrasonic vibrating screen ensures that even sticky or agglomerated calcium oxide particles are effectively separated, maintaining flow and output.