In pharmaceutical manufacturing, precision, purity, and safety are non-negotiable. Whether producing tablets, capsules, or powder formulations, manufacturers must adhere to strict GMP (Good Manufacturing Practice) standards. One of the most critical aspects of this process is powder screening. Fine powders must be separated according to particle size while avoiding contamination, segregation, or material degradation. For this purpose, the airflow vibrating screen stands out as a top-tier solution, particularly for lightweight, ultrafine pharmaceutical powders.
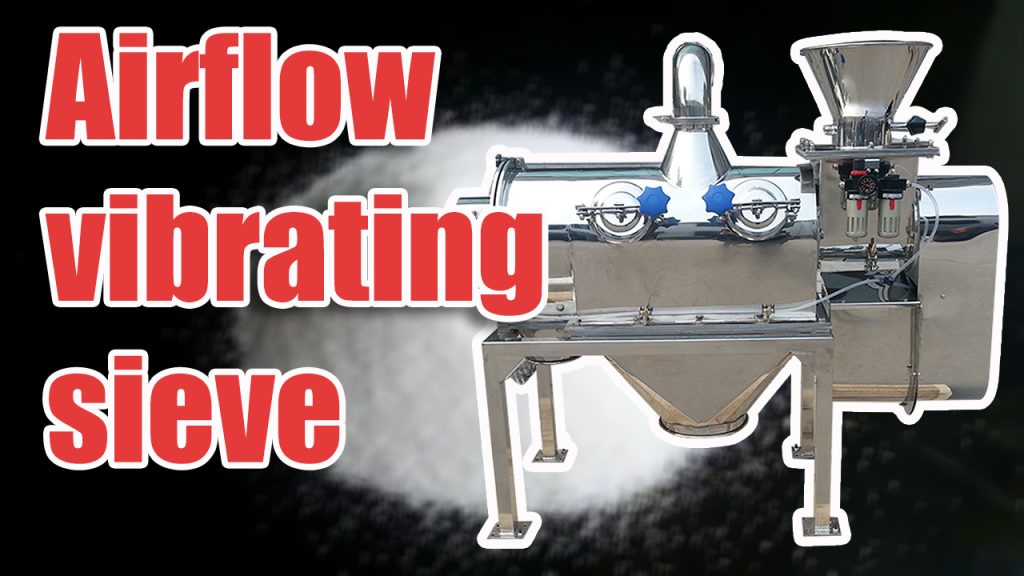
Also referred to as a horizontal airflow sieve or centrifugal sifter, the airflow vibrating screen uses a high-speed rotor and air flow to propel powder particles through a cylindrical mesh. Unlike traditional vibrating screens, this system relies on airflow velocity rather than direct vibration, making it exceptionally gentle on sensitive and cohesive materials.
This type of screen is particularly suited for pharmaceutical powders such as:
- Antibiotic base powders
- Herbal extracts
- Nutraceuticals
- Fine APIs (Active Pharmaceutical Ingredients)
These powders often have low bulk density, electrostatic properties, and hygroscopic behavior. Conventional vibratory screens may fail to process them efficiently due to clogging, material build-up, or static adhesion. In contrast, the airflow vibrating screen maintains consistent separation by fluidizing the powder and evenly distributing it across the screen mesh.
The benefits of airflow screening in the pharmaceutical sector are numerous:
- Gentle Screening Process: The absence of mechanical vibration ensures no degradation or alteration of delicate compounds.
- High Throughput: The screen can process 500–1500 kg/h of material, depending on mesh size and powder flow properties. For example, a 1450mm airflow screen can process 1000 kg/h of 200 mesh herbal powder with ease.
- Dust-Free Operation: Fully enclosed stainless steel construction ensures no dust escape, protecting both operators and product integrity.
- Compliance: The screen meets cGMP, FDA, and hygiene standards, making it suitable for cleanroom use.
Airflow vibrating screens typically support mesh sizes ranging from 80 mesh (180 microns) to 500 mesh (25 microns), making them ideal for both coarse and ultra-fine powder classification. The high rotational speed of the internal blade assembly combined with air turbulence enables materials to pass through the screen rapidly without binding.
Another unique advantage is continuous operation. The screen supports inline installation, allowing direct integration with upstream grinding or drying systems and downstream packaging or mixing equipment. This integration reduces manual handling, improves efficiency, and minimizes the risk of cross-contamination.
The airflow vibrating screen is also easy to maintain and operate. The design features quick-disassembly clamps and tool-free access, enabling screen changes and cleaning within minutes. For pharmaceutical production lines requiring frequent product switches, this ease of use is a major benefit.
In addition, the unit consumes less power compared to traditional vibrating screens, contributing to overall energy savings. The screen is often equipped with intelligent control systems to regulate speed, monitor pressure, and automate feeding.
In conclusion, the airflow vibrating screen is a vital tool for the pharmaceutical industry. Its ability to screen ultra-fine, sensitive powders at high throughput levels, combined with compliance to international health standards, makes it an indispensable machine for pharmaceutical manufacturing environments. Its role in ensuring product quality, operational safety, and regulatory compliance cannot be overstated.