In the world of material processing, optimizing screening efficiency is critical to ensuring consistent product quality, high throughput, and reduced operational costs. The HXS-1536 Square Swing Screen, a type of gyratory or swing sieve, is an excellent choice for many industries requiring high screening capacity and precise separation of materials. This advanced screening machine is designed to deliver a more reliable and consistent screening process compared to traditional vibrating screens, especially for materials that are prone to clustering or require gentle handling. But how can operators improve the material screening output when using the HXS-1536 square swing screen? Here are several strategies to optimize its performance and maximize output.
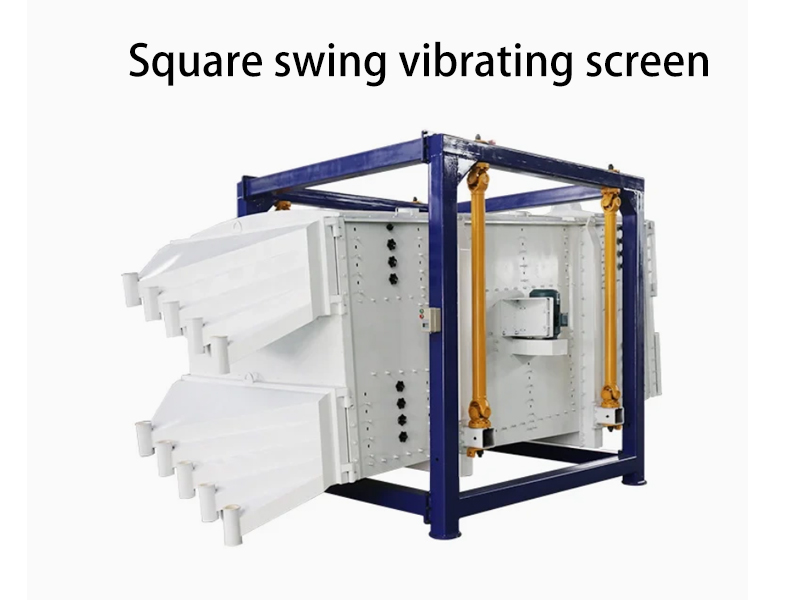
1、Select the Correct Mesh Size
One of the most important factors in improving the output of any screening system is choosing the appropriate mesh size for the material being screened. For the HXS-1536 Square Swing Screen, selecting the correct mesh size ensures that the material flows smoothly and is adequately separated.
- Finer mesh for finer materials: If you're working with fine powders or particles, make sure to use a mesh size that matches the material’s particle size. Using a mesh that is too small may slow down the screening process and lead to clogging.
- Coarser mesh for larger particles: For larger or more granular materials, select a mesh size that accommodates the particle size, allowing efficient separation without overloading the screen.
Choosing the right mesh size will ensure that the screen is optimized for your material's specific characteristics, improving overall efficiency and throughput.
2、Adjust the Amplitude and Vibration Intensity
The HXS-1536 Square Swing Screen allows operators to fine-tune the amplitude and vibration intensity, which can have a direct impact on material separation. The amplitude refers to the distance that the screen surface moves, and adjusting it can influence how effectively the material moves across the screen.
- Increase amplitude for larger or heavier materials: If you are screening larger or denser materials, increasing the amplitude can help the material move more easily across the screen, reducing clogging and promoting higher output.
- Decrease amplitude for fine or light materials: For finer particles, reducing the amplitude helps to prevent excessive bouncing or disruption of delicate materials, thus improving precision and flow through the screen.
Experimenting with different amplitudes based on your material type can improve the screening efficiency and, in turn, boost the output.
3、Optimize Feed Rate and Material Distribution
The rate at which material is fed into the HXS-1536 Square Swing Screen significantly affects screening performance. If the material is fed too quickly, the screen may become overloaded, leading to inefficient separation and reduced output. Conversely, feeding the material too slowly can also result in lower throughput.
- Ensure uniform material distribution: The material should be evenly distributed across the screen surface for optimal performance. Any imbalance can result in clogged or overloaded sections of the screen, reducing efficiency.
- Adjust the feed rate: Adjust the feed rate to match the capacity of the screen and the material's characteristics. Avoid overloading the screen, as this can lead to lower screening efficiency, increased wear on the machine, and higher maintenance costs.
To achieve the best results, consider using a feeder that ensures a consistent and uniform flow of material onto the screen.
4、Regular Cleaning and Maintenance
Another essential strategy to improve the screening output with the HXS-1536 Square Swing Screen is to maintain the equipment regularly. Clogged screens, worn-out parts, or accumulated material on the sieve surface can significantly hinder the performance of the screen.
- Clean the mesh regularly: For materials that are sticky or have a tendency to clump, the mesh may become blocked over time. Regular cleaning helps ensure that the screen surface remains clear and the material can flow freely.
- Check and replace wear parts: Regularly inspect critical parts such as the motor, bearings, and springs. Worn or damaged parts should be replaced promptly to avoid downtime and reduce maintenance costs.
Proper and timely maintenance ensures that the screen runs smoothly and maximizes its operational efficiency.
5、Optimize the Swing Angle and Screen Motion
The motion and swing angle of the HXS-1536 Square Swing Screen are crucial factors in determining how material moves through the system. The unique elliptical motion of the swing screen mimics the natural flow of materials and provides better distribution across the screen surface.
- Adjust the swing angle: By fine-tuning the swing angle, you can control how the material moves on the screen. A larger swing angle allows for more material movement and a faster throughput, while a smaller swing angle may provide better control and precision for finer materials.
- Use the optimal motion: The machine’s motion is designed to minimize material jamming and clogging, so finding the optimal settings for your specific material can enhance separation and increase output.
Experimenting with different settings for swing angle and motion will help you find the best configuration for maximum screening output.
6、Consider the Material Characteristics
The HXS-1536 Square Swing Screen is especially effective for handling fragile, sticky, and fine materials. However, each material behaves differently, and understanding these behaviors can help you better adapt the screen settings for improved output.
- Sticky materials: For sticky materials, consider using a mesh with a coating or a mesh type that is less likely to clog. You can also reduce the feed rate and increase the vibration intensity to help prevent sticking.
- Fine or light materials: Fine powders or materials that are prone to agglomeration may benefit from lower vibration amplitudes and more gradual feeding to improve screening efficiency.
- Moisture-sensitive materials: For wet materials or those prone to clumping, using a gentle screening process and ensuring that moisture levels are within an optimal range can help improve material flow.
Tailoring the screen settings to the specific characteristics of the material can go a long way in improving output.
7、Utilize Multiple Screening Stages (if necessary)
In some cases, a single stage of screening may not be sufficient to meet the desired material purity or throughput. The HXS-1536 Square Swing Screen can be configured for multi-stage screening, which can be especially useful for applications where precise material classification is required.
- Multi-stage separation: By adding additional stages of screening, you can separate different particle sizes more effectively, resulting in higher output and more consistent product quality.
- Progressive screening: The material can be screened in stages, starting with a coarse separation and progressing to finer screens for greater precision.
Multi-stage screening allows for greater control over the screening process, improving the overall efficiency and capacity of the system.