How to use airflow vibrating sieve to improve diatomaceous earth filtration efficiency?
Post Date: 2025-03-07
Diatomaceous earth (DE) is a versatile material widely used in filtration applications across industries such as food and beverage, pharmaceuticals, water treatment, and chemicals. Its high porosity and adsorption properties make it an excellent filtration medium. However, to maximize its efficiency, the particle size and uniformity of diatomaceous earth must be carefully controlled. This is where airflow vibrating sieves come into play.
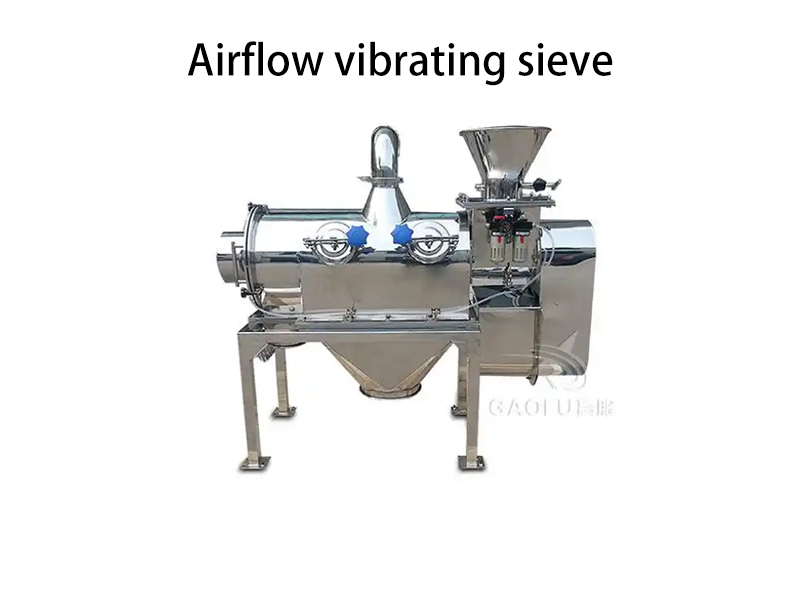
In this article, we will explore how airflow vibrating sieves can improve the filtration efficiency of diatomaceous earth and the key steps to optimize their use.
- Understanding the Role of Particle Size in Diatomaceous Earth Filtration
The filtration efficiency of diatomaceous earth largely depends on the particle size distribution. Smaller particles provide a larger surface area for adsorption, while larger particles help maintain the flow rate. Achieving the right balance is critical.
- Too fine particles: May clog the filter, reducing flow rate and increasing pressure drop.
- Too coarse particles: May compromise filtration quality, allowing impurities to pass through.
An airflow vibrating sieve ensures precise particle size control, enabling optimal filtration performance.
2. How Airflow Vibrating Sieves Work
Airflow vibrating sieves are advanced screening machines that combine vibration and airflow to separate particles based on size. Here’s how they work:
- Vibration Mechanism: The sieve uses high-frequency vibrations to move particles across the screen mesh, ensuring efficient separation.
- Airflow Assistance: A controlled airflow is introduced to fluidize the material, reducing clogging and improving screening accuracy.
- Multi-Layer Screening: Some models feature multiple screen layers to classify particles into different size fractions simultaneously.
This combination of vibration and airflow makes airflow vibrating sieves ideal for handling lightweight, fine, and adhesive materials like diatomaceous earth.
3. Benefits of Using Airflow Vibrating Sieves for Diatomaceous Earth
- Improved Particle Size Control: Achieve precise particle size distribution for optimal filtration performance.
- Higher Screening Efficiency: The airflow prevents mesh clogging, ensuring continuous operation.
- Reduced Waste: Accurate screening minimizes the loss of usable material.
- Enhanced Filtration Quality: Consistent particle size leads to better filtration results.
- Energy Efficiency: Airflow vibrating sieves consume less energy compared to traditional screening methods.
4. Steps to Use Airflow Vibrating Sieve for Diatomaceous Earth Filtration
Step 1: Select the Right Screen Mesh Size
Choose a screen mesh size that matches the desired particle size range for your filtration application. For diatomaceous earth, mesh sizes typically range from 100 to 400 mesh (150–38 microns).
Step 2: Adjust Vibration Frequency and Amplitude
Optimize the vibration settings to ensure efficient particle movement without damaging the material. Higher frequencies are suitable for fine particles, while lower frequencies work better for coarser particles.
Step 3: Control Airflow Rate
Adjust the airflow to fluidize the diatomaceous earth without blowing it away. Proper airflow ensures smooth material flow and prevents clogging.
Step 4: Perform Regular Maintenance
Clean the sieve regularly to prevent mesh blockage and ensure consistent performance. Check for wear and tear on the screen mesh and replace it as needed.
Step 5: Monitor and Optimize
Continuously monitor the screening process and make adjustments to vibration, airflow, and feed rate to achieve the best results.
5. Applications of Airflow Vibrating Sieves in Diatomaceous Earth Filtration
- Food and Beverage Industry: For filtering beer, wine, and juices.
- Pharmaceuticals: For purifying liquids and separating fine powders.
- Water Treatment: For removing impurities from water.
- Chemicals: For catalyst recovery and liquid filtration.