The rotary vibrating screen in the chemical industry can work continuously for 24 hours.
Post Date: 2025-02-04
The Role of Rotary Vibrating Screens in Continuous Operation in the Chemical Industry
In the modern chemical industry, efficiency, reliability, and consistent product quality are essential. Rotary vibrating screens play a crucial role in ensuring these factors, particularly when it comes to material separation, classification, and filtration. One of the standout features of rotary vibrating screens is their ability to operate continuously, often running 24 hours a day, without significant degradation in performance.
What is a Rotary Vibrating Screen?
A rotary vibrating screen, often referred to as a vibrating sifter or sieve, is a piece of equipment designed to separate bulk materials according to size, shape, and other characteristics. The vibrating motion is produced by a motor, which drives a set of screens in a circular motion, causing the material to pass through mesh screens that filter particles based on size.
These screens are typically used to separate fine powders, granular materials, and liquids, and can handle both wet and dry materials. In the chemical industry, rotary vibrating screens are commonly employed for tasks such as:
- Screening raw materials before processing
- Filtering chemicals or solvents
- Classifying finished products
- Removing impurities or contaminants from products
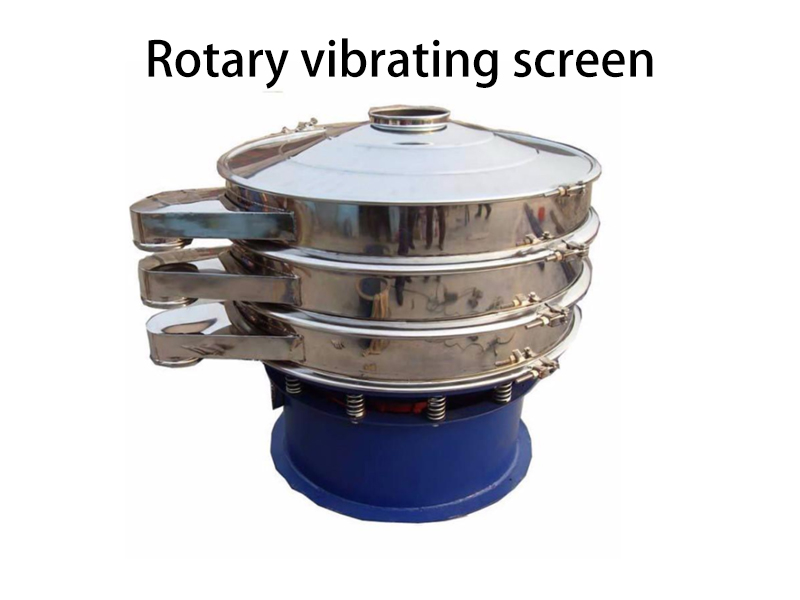
Why is Continuous Operation Important?
The chemical industry often deals with large volumes of materials and products that require constant processing. Whether it’s ensuring a steady supply of raw materials or maintaining a consistent product quality, continuous operation of equipment like rotary vibrating screens ensures minimal downtime and maximized productivity.
Here’s why 24-hour operation is so important:
1、High Efficiency and Throughput: Rotary vibrating screens are designed to handle high volumes of material with minimal effort. Their continuous operation allows for increased throughput without sacrificing accuracy or precision in separation.
2、Reduced Downtime: By operating continuously, these screens help minimize stoppages in the production process. This is particularly crucial in industries where time-sensitive production schedules and high-volume production are the norms.
3、Consistent Product Quality: Continuous screening ensures that only materials that meet specific quality standards are used in production. This leads to better consistency in the final product and reduces the risk of defects or impurities.
4、Labor and Energy Efficiency: Rotary vibrating screens can operate with minimal human intervention once set up correctly. Their automation capabilities help reduce labor costs, while their energy-efficient design ensures that the system does not require excessive power to function effectively over long periods.
5、Versatility: Whether it’s handling different chemical formulations, diverse product sizes, or varying production volumes, rotary vibrating screens can adapt to multiple applications. Their ability to run non-stop makes them especially versatile for large-scale operations that demand uninterrupted screening.
How Does a Rotary Vibrating Screen Achieve Continuous Operation?
The continuous functionality of a rotary vibrating screen is made possible by a combination of durable construction and efficient design. Here are some key elements that enable these machines to work 24/7:
- Durable Build: Made from robust materials such as stainless steel, rotary vibrating screens are designed to withstand the wear and tear associated with continuous use. Their solid construction ensures longevity and minimizes maintenance needs.
- Vibration Mechanism: The vibrating action is created by a motor that generates a three-dimensional motion (horizontal, vertical, and tilt). This continuous motion is critical for maintaining a steady flow of material through the mesh screen.
- Self-Cleaning Capabilities: Many modern rotary vibrating screens come with self-cleaning functions. This feature is particularly important in chemical applications, as it helps to prevent clogging of the mesh with sticky or adhesive particles, ensuring uninterrupted performance.
- Adjustable Parameters: Operators can adjust the vibration amplitude, screen inclination, and other settings to optimize the performance for different types of material. This adaptability ensures that the screen can efficiently process varying materials over extended periods.
- Minimal Maintenance: With proper maintenance schedules, rotary vibrating screens require little intervention during continuous operation. Regular checks for wear and tear, as well as cleaning, help to ensure their smooth functioning.
Applications in the Chemical Industry
In the chemical industry, rotary vibrating screens are used in various stages of production:
- Raw Material Screening: Before chemical reactions or manufacturing processes begin, raw materials must be screened to ensure they meet the required specifications. This helps prevent issues like clogs or contamination down the production line.
- Powder and Granule Separation: Chemical powders and granules often require specific size classification. Rotary vibrating screens efficiently separate these materials to ensure that the right product is used in further processing.
- Liquid Filtration: When processing chemical liquids, rotary vibrating screens are used to filter out solid contaminants, ensuring purity in the final product.
- Packaging and Final Product Inspection: After chemicals have been processed, they must often undergo final quality checks before packaging. Rotary vibrating screens are used in these stages to remove any last contaminants and ensure a high-quality, clean product.