Three-Layer Tumbler Screen for Rubber Powder: High Accuracy and Continuous Operation.
Post Date: 2025-05-12
In the field of fine powder classification, especially when dealing with delicate or sticky materials such as rubber powder, traditional high-frequency vibrating screens often fall short—causing mesh clogging, inefficient separation, and material degradation. For these applications, the Tumbler Vibrating Screen stands out as a superior solution.
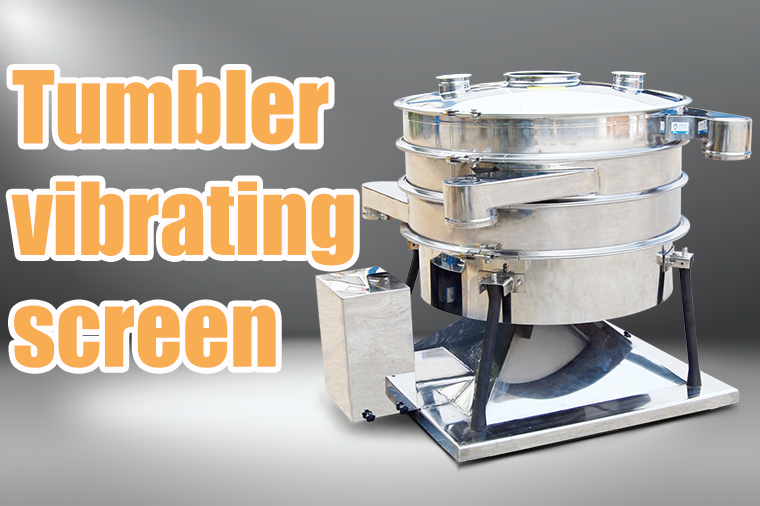
Mimicking the gentle motion of manual sieving, the tumbler vibrating screen is a low-frequency, high-precision screening machine designed specifically for efficient grading of fine and ultra-fine materials. When applied to rubber powder separation, it delivers exceptional performance in terms of accuracy, screen cleanliness, and uninterrupted operation.
- What Is a Tumbler Vibrating Screen?
The tumbler vibrating screen, also known as a swing screen, is a type of screening equipment that simulates manual sieving through a gentle elliptical motion combined with a slight vertical throw. This screening technique avoids the harsh vibration of traditional rotary or linear screens, offering a more refined and energy-efficient approach to fine material classification.
Key structural features:
- Three-layer screen deck design for multi-grade separation
- Circular and elliptical combined motion
- Multiple mesh cleaning mechanisms: bouncing balls, ultrasonic systems, rotating brushes
- Fully enclosed structure to prevent dust leakage
- Designed for Rubber Powder Classification
Rubber powder, produced from recycled tires or rubber granulation processes, has unique handling challenges:
- It is lightweight and often carries electrostatic charge
- It tends to clump or stick to mesh surfaces
- It requires precise size distribution for use in playgrounds, asphalt, rubber mats, and industrial fillers
The tumbler vibrating screen’s gentle motion ensures the rubber powder remains intact, while its multi-layer configuration enables classification into three or more size fractions in a single pass.
- Three-Layer Deck Configuration for Graded Separation
This particular model features a three-deck system, allowing it to separate rubber powder into four different size grades. For example:
- Top layer: >1.0 mm granules
- Middle layer: 0.5–1.0 mm particles
- Bottom layer: 0.2–0.5 mm powder
- Undersize: <0.2 mm fines
The multiple decks improve processing efficiency and allow operators to tailor the output for various end uses, such as playground surfacing, rubber sheets, or modifiers for road construction.
- Multiple Screen Cleaning Systems: No Clogging, No Downtime
One of the standout features of the tumbler vibrating screen is its advanced screen cleaning functionality. The combination of bouncing rubber balls, brush systems, and (optionally) ultrasonic mesh cleaning ensures that rubber powder particles do not clog the mesh.
Advantages of these systems include:
- Continuous self-cleaning during operation
- Consistent throughput and screen efficiency
- Reduced manual intervention and cleaning shutdowns
For electrostatically charged rubber powder, ultrasonic cleaning significantly reduces sticking and maintains mesh permeability.
- 24/7 Continuous Operation with Minimal Maintenance
Unlike traditional screening machines that may overheat or wear quickly under extended use, the tumbler vibrating screen is engineered for continuous, long-duration processing. It features:
- Balanced motion to minimize stress on bearings
- Efficient power consumption (typically 2–5.5 kW depending on size)
- Wear-resistant components that extend service intervals
- Enclosed design for safe, dust-free operation
Many factories run the machine 24 hours a day with only short pauses for inspection and mesh replacement after hundreds of operating hours.
- High Screening Accuracy and Yield
The tumbler vibrating screen provides up to 95% screening efficiency even for rubber powders smaller than 200 microns. The slow, controlled motion ensures particles are fully exposed to the mesh surface, increasing the probability of passing through the appropriate aperture.
Processing capacity varies based on material flow and mesh sizes, but a typical three-layer unit can handle:
- 500 to 1200 kg/hour for rubber powder (depending on moisture, mesh, and deck size)
- Environmental and Safety Considerations
The tumbler screen is often supplied with:
- Fully sealed covers and dust extraction ports
- Low-noise operation (<70 dB)
- Easy-to-clean stainless steel frames for hygiene compliance in sensitive applications