In the field of fine material processing, especially in the production and classification of metal powders, the demand for precision sieving technology has grown significantly. One such advanced solution is the ultrasonic vibrating screen, which has proven to be particularly effective in sieving alloy powders. The primary goal of this process is to enhance the purity of the material, which directly impacts the performance, quality, and value of the final product.
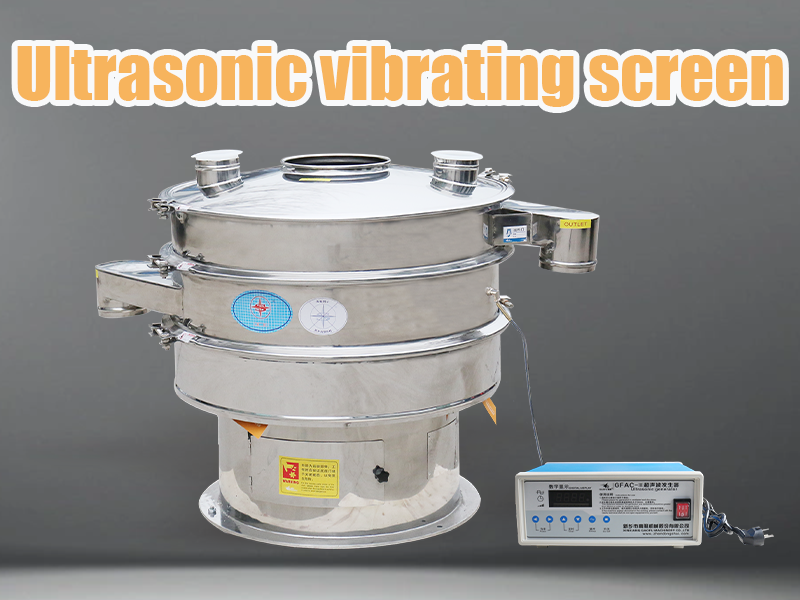
Why Alloy Powder is Challenging to Sieve
Alloy powders are widely used in industries such as additive manufacturing (3D printing), metallurgy, aerospace, electronics, and more. However, their unique physical properties make them difficult to sieve using traditional screening methods. These challenges include:
- Strong adsorption between particles, causing them to clump together.
- High cohesiveness, which makes particles stick to the screen surface or to each other.
- Sticky and viscous nature, leading to screen clogging.
- High electrostatic charge, resulting in erratic particle movement.
- High density, which limits particle stratification during vibration.
- Extremely fine particle sizes, which are often below 100 microns and hard to separate with precision.
These properties reduce screening efficiency, cause material loss, and often result in inconsistent particle sizes that do not meet application requirements.
The Role of Ultrasonic Vibrating Screens
To address these challenges, ultrasonic vibrating screens integrate high-frequency ultrasonic waves into the traditional vibrating screen framework. This technology creates micro-vibrations on the screen surface, which helps to break the surface tension of fine particles, effectively preventing clogging and enabling better particle dispersion.
This results in several significant advantages:
- Improved Sieving Precision:
The ultrasonic system significantly boosts screening accuracy, with precision increased by more than 80% compared to conventional methods. This means a higher yield of target-sized particles and reduced contamination from oversize or undersize materials. - Enhanced Material Flow:
The added ultrasonic energy keeps the mesh clean and allows fine powders to pass through more freely. This is especially important for ultrafine powders, where traditional screens would be blocked. - Effective Screening of Difficult Materials:
Materials with strong adsorption, high viscosity, high electrostatic charge, or high density—all common characteristics of alloy powders—can now be screened efficiently. - Reduced Downtime and Maintenance:
Since ultrasonic screens remain cleaner during operation, there is less need for manual cleaning or screen replacement, minimizing downtime and reducing maintenance costs. - Customizable Design:
Ultrasonic vibrating screening equipment can be fully customized to meet specific production requirements, such as mesh size, capacity, material construction, and integration with existing systems.