Why can ultrasonic vibrating screen solve the problem of screening materials that are easy to clumping and have strong viscosity?
Post Date: 2025-02-04
In industries such as food processing, pharmaceuticals, chemicals, and minerals, the screening of powders and particles is a critical step to ensure quality and efficiency. However, certain materials can present significant challenges in the screening process, especially when they have a tendency to clump together or exhibit strong viscosity. These materials can clog conventional screens, reducing productivity, and sometimes leading to poor separation results. This is where ultrasonic vibrating screens come into play. By utilizing high-frequency sound waves, ultrasonic vibrating screens offer a solution to these common issues, ensuring smoother, more efficient material separation.
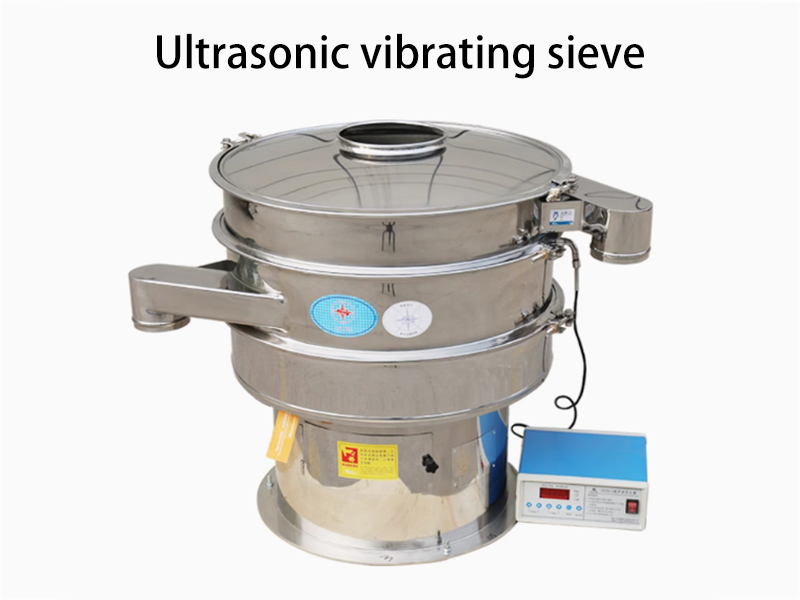
The Problem with Clumping and High Viscosity Materials
Clumping, or agglomeration, occurs when particles stick together due to moisture, electrostatic charges, or cohesive forces. Materials that are prone to clumping can quickly clog traditional vibrating screens, leading to a reduction in throughput and increased maintenance time. Similarly, materials with strong viscosity, such as certain wet powders or sticky substances, tend to cling to the screen mesh, impeding the flow of the material and leading to incomplete separation.
In both cases, the traditional vibrating screening system might not be sufficient to achieve the desired results, especially when fine particles or powders need to be separated or classified.
How Ultrasonic Vibrating Screens Work
Ultrasonic vibrating screens integrate a specialized ultrasonic transducer system with a conventional vibrating screen. The ultrasonic transducer generates high-frequency sound waves (typically in the range of 20 kHz to 40 kHz) that are transmitted through the mesh screen. These sound waves cause the mesh to vibrate at a very high rate, reducing friction between the material particles and the screen surface. The ultrasonic energy promotes smoother material movement and prevents clogging by breaking up clumps or agglomerates.
These ultrasonic waves help to:
1、Reduce the Surface Tension: The high-frequency vibrations break up the surface tension between the particles, which is often the cause of clumping and sticking.
2、Increase the Screening Efficiency: With the ultrasonic waves reducing particle adhesion to the mesh, the particles pass through the screen more easily, increasing the efficiency of the screening process.
3、Prevent Clogging and Blockage: The ultrasonic waves prevent fine, sticky, or viscous particles from sticking to the screen surface, ensuring that the mesh remains clear and the material flows freely.
4、Improve Separation of Fine Particles: Ultrasonic vibrations are especially beneficial for screening fine particles that are more likely to clog the screen. The gentle agitation helps to keep these fine materials in motion, enabling them to pass through the mesh more easily.
5、Enhance Processing Time: With the prevention of clumping and sticking, the entire screening process becomes faster and more efficient, reducing the time needed for material processing and increasing overall productivity.
Applications in Various Industries
Ultrasonic vibrating screens are especially useful in industries dealing with materials that are prone to agglomeration or have high viscosity. Some examples of materials and applications that benefit from ultrasonic vibrating screens include:
- Pharmaceuticals: Powdery substances like active pharmaceutical ingredients (APIs) or excipients often have a tendency to clump. Ultrasonic screens help ensure smooth separation and classification of these powders.
- Food Processing: Sticky powders such as flour, starch, or sugar can clog traditional screens, but ultrasonic vibrating screens help prevent this, ensuring better separation and higher production rates.
- Chemicals and Paints: Viscous or sticky chemical substances, such as pigments or resins, can be challenging to screen without clogging. Ultrasonic vibrating screens help maintain the flow of these materials during processing.
- Mineral Processing: Fine mineral powders and other granular materials can become compacted or agglomerated during screening, but ultrasonic technology ensures better performance by reducing particle adhesion.