Yield and purity increased by two times: Graphite powder ultrasonic vibrating screen.
Post Date: 2025-04-30
In the production and processing of high-performance graphite powders, maintaining material purity and achieving precise particle size distribution are crucial to ensuring product quality and meeting application-specific requirements. Graphite is widely used in industries such as energy storage (especially in lithium-ion batteries), metallurgy, electronics, lubricants, and advanced composites. However, due to its fine and lightweight nature, traditional screening methods often struggle with clogging and poor separation accuracy. To overcome these challenges, many manufacturers are now turning to ultrasonic vibrating screen—a cutting-edge solution designed to deliver exceptional performance in fine powder screening.
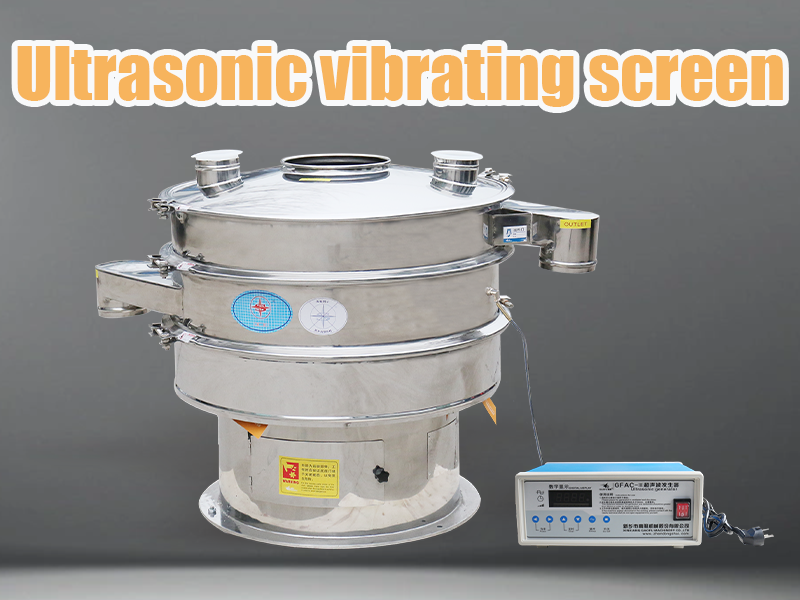
The ultrasonic vibrating screen combines traditional vibratory screening with a high-frequency ultrasonic system, which superimposes micro-vibrations onto the screen mesh. This technology dramatically reduces mesh blinding, ensuring that fine powders like graphite can pass through the screen more efficiently and without blockage. One of the key benefits of this system is its ability to maintain a clear screen surface, even when dealing with ultra-fine or sticky powders that would otherwise cause frequent downtime and maintenance in conventional screens.
When applied to graphite powder screening, ultrasonic vibrating screens offer several outstanding advantages:
- Improved Material Purity: The equipment effectively removes contaminants and oversized particles, enhancing the purity of the final graphite product. This is especially important for applications in battery anodes, where high purity is critical for performance and safety.
- No Mesh Clogging: The ultrasonic system prevents material build-up on the mesh, allowing for consistent throughput and avoiding the need for frequent cleaning or screen replacement.
- Significant Increase in Yield: By maintaining open screen apertures and reducing material loss, ultrasonic screening can increase screening output by up to 2 times, compared to standard vibrating screens. This leads to higher productivity and better return on investment for manufacturers.
- Low Noise Operation: Despite its high-frequency capability, the ultrasonic vibrating screen operates with minimal noise, creating a more comfortable and safe working environment for operators.
- Precision Screening: Ultrasonic vibrations enable more accurate classification of graphite particles, ensuring consistent particle size distribution that is essential for high-end industrial applications.
In addition, the equipment is flexible in design, allowing for customization in mesh sizes and screen layers depending on processing needs. It integrates well into both small-scale and high-volume production lines, making it a versatile tool for manufacturers working with powdered graphite.